Samsung SDI, Hyundai and Kia partner on high-performance batteries for robots
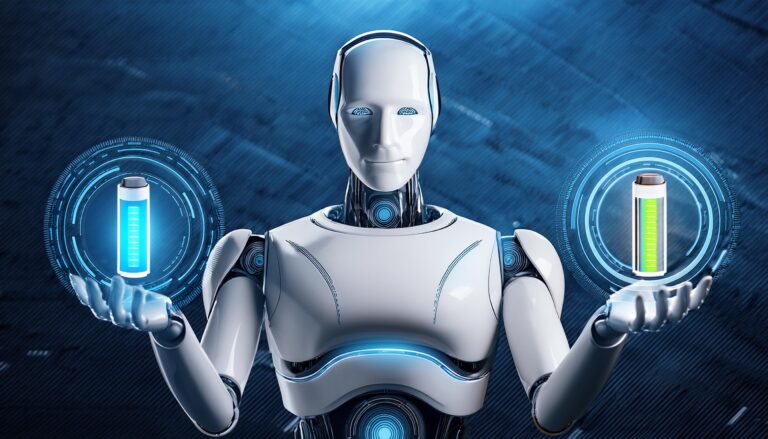
Batteries for bots
Hyundai Motor, Kia, and Samsung SDI recently announced a partnership to develop high-performance batteries specifically designed for robots. This collaboration, formalized through a memorandum of understanding signed on February 24, 2025, aims to create advanced battery solutions that enhance energy density, output and usage time for robotic applications.
The initiative addresses the challenge of limited battery space in robots, where current options – often adapted from electric vehicles or powertools – are not optimized for robotic needs.
As per the partnership, Samsung SDI will focus on developing high-capacity battery active materials and efficient cell and pack designs, while Hyundai and Kia’s Robotics Lab will test and refine these batteries for practical use in robots.
This move builds on the three companies’ existing ties with Samsung SDI already poised to supply EV batteries to Hyundai from next year, and reflects a broader push by the trio into the growing robotics market (see recent Adamas whitepaper).
The partnership is seen as a necessary step toward development of innovative, specialized battery solutions for Hyundai and Kia’s expanding robotics ventures, including exoskeletons and service robots.
Why EV batteries don’t cut it
Conventional lithium-ion batteries, while versatile and widely used in devices like electric vehicles, often fall short for robots due to a few key limitations tied to the unique demands of robotic systems.
First, robots typically have tight space constraints. Unlike electric vehicles with room for large battery packs, robots – especially smaller or humanoid varieties – need extra compact power sources.
Conventional lithium-ion batteries, designed for higher-capacity applications, can be bulky or awkwardly shaped, making them tough to integrate into a robot’s frame without sacrificing design efficiency or agility.
Second, energy density and output can be mismatched for robotic needs. Robots often require quick bursts of high power for movements like lifting or rapid locomotion, alongside sustained energy for longer operation. Standard lithium-ion batteries, optimized for steady discharge EVs (i.e., sipping rather than gulping), may not deliver the peak power fast enough or efficiently enough for these dynamic tasks, leading to performance bottlenecks.
Third, usage time and recharge cycles matter more in robotics. Many robots, like service or industrial models, need to operate for extended periods without frequent recharging, but conventional batteries may not balance longevity and performance well under the variable loads robots experience. This can mean shorter operational windows or faster degradation, which isn’t ideal for practical deployment.
Lastly, conventional designs aren’t tailored to the diversity of robotic applications. Exoskeletons, drones or autonomous delivery bots each have distinct power profiles, and off-the-shelf lithium-ion batteries – often borrowed from power tools or EVs – aren’t fine-tuned for these specialized roles. This lack of optimization can limit a robot’s effectiveness or force trade-offs in functionality.
Focus on form factors and active materials
On the cell chemistry side, cathode and anode materials could shift to meet robots’ needs for higher power density, faster discharge rates or longer life under irregular loads. Standard lithium-ion cathodes – like nickel-cobalt-manganese (NCM) in EVs – might not cut it over the medium- to long-term.
For robots needing rapid power bursts, something like lithium-iron-phosphate (LFP) could be adapted for its stability and quick discharge, though it’s less energy-dense. Alternatively, super-high-nickel NCM variants or even emerging options like lithium-sulfur (Li-S) might come into play for better energy density and lighter weight.
On the anode end, graphite’s the norm now, but silicon-based anodes (which store more lithium) or even lithium metal (for next-gen energy density) could get prioritized to squeeze more juice into tight spaces. These tweaks would aim to balance power, capacity and durability, depending on whether the robot’s hauling cargo or assisting humans.
Form factors are where things get really interesting. Conventional cylindrical (like 18650 cells) or prismatic cells work fine for cars or gadgets, but robots often need odd shapes to fit into a cramped, irregular chassis. Custom pouch cells – flexible, lightweight, and moldable – could dominate here, letting designers contour batteries around a robot’s joints or frame.
Thin, flat stacks might suit humanoid bots, while tiny, modular cells could power distributed systems in swarm robots. Solid-state batteries, with their potential for custom shaping and higher safety, might also emerge as a game-changer, ditching bulky liquid electrolytes for a denser, more robot-friendly package.
The partnership between Hyundai, Kia and Samsung SDI suggests they’re eyeing this kind of specialization. They’re not just slapping EV batteries into robots – they’re rethinking the chemistry and form to match the weird, wild demands of robotics. Expect bespoke solutions for specific applications, not off-the-shelf fixes.
No one-size-fits-all solution
NiMH: Only practical for low-stakes, rugged robots where weight’s not a dealbreaker – think slow agricultural helpers.
LFP: A workhorse for reliable, long-haul robots where safety trumps density – industrial or static bots.
LMFP: A sweet spot for safe, durable robots where cost and space matter – like warehouse or service bots—but not the go-to for max performance.
NCM 6-Series: The middle ground, good for versatile robots but outclassed by specialized options.
NCM 9-Series: The premium pick for high-end robotics (drones, exoskeletons) needing lightweight power, if you can manage the risks.
Silicon Anode: A wildcard – pairs with any cathode to shrink size, but its instability limits it to cutting-edge designs until stabilized.
For robotics, the choice hinges on the bot’s job: NCM 9-series for performance, LMFP or LFP for durability, NiMH for niche toughness. Anodes like silicon could tip the scales if applied smartly, but they’re still maturing. Hyundai and Kia’s battery push might lean toward NCM 9 or LMFP, balancing innovation with practicality.
Join us at Rare Earth Mines, Magnets & Motors 2025
Join us in Toronto in September 2025 for Rare Earth Mines, Magnets & Motors 2025 where we’ll dive into the outlook for robotics with leading industry experts.
The two-day event will bring together business and technical leaders from across the global mine-to-OEM supply chain for high caliber discussions and networking at a 5-star venue.
Key themes of this year’s conference will include robotics, automation, advanced air mobility, and the emerging mine-to-magnet supply chain coming together upstream.
Special guest: Steve Wozniak, co-founder of Apple
More information: www.adamasevent.com